|
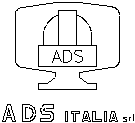 |
LBT PROJECT 2x8.4m TELESCOPE |
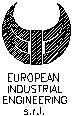 |
TECHNICAL SPECIFICATION
FOR
ROTATING ENCLOSURE GEARS AND MOTORS |
Doc. 301S001/A November 5, 1997
W. Gallieni and S. DeRigne |
- INDEX :
0 - Introduction.
1 - Supply Description.
2 - Environmental Conditions.
2 - Delivery Conditions.
The four Rotation Bogies of the Large Binocular Telescope
co-rotating enclosure require a total of 8 driving units (a pair of
driving units for each corner bogie), plus one spare unit, for a total
of 9 driving units. Each driving unit will be composed of a gear
reduction unit, a motor with brake and a power inverter for variable
speed control. These individual components are described below.
For all the mechanical data used for the driving units dimensioning
and selection, please refer to the Technical Report
Doc. No. 301a002d. Those data have driven us to a first selection of 8
gear reduction units of the hollow shaft type, with overall
transmission ratio 1 : 315, and nominal low speed shaft torque of
40000 Nm. These will be driven by 8 squirrel cage motors supplying
12,5 KW, complete with disc brake (DC actuated). The motors have been
specified as over-sized from 16 HP to 20 HP to minimize the problems
of overheating when operating at low speed. The motors will be
supplied with external forced ventilation for cooling during low-speed
operation. The brakes will be operable independently from the motor
power. We prefer to have either 4 or 8 VFD units supplying individual
motors or pairs of motors.
1.1 Gear Boxes
The 8 driving units (plus one spare) will be of the hollow shaft type,
right angle, vertical mount, complete with coupling and flange for the motor
connection and support; Size 315, quadruple reduction, overall
transmission ratio 1 : 315, nominal low speed shaft torque = 40000 Nm ---
as per the catalogue of the GSM Company, in Modena, ITALY or equivalent.
G.S.M. MODENA
via Dino Lugli, no. 12
42100 Modena
ITALY
telephone: 39-59-365022
telefax: 39-59-280792
The locking of the gear hub on the wheel shaft must be realized in the
version with RINGFEDER locking conical rings, as per the illustrations
of the GSM catalogue enclosed. The verification of the gear size has
to be done by the Manufacturer taking into account over the demanded
torque, of the environmental conditions where the enclosure shall be
installed as listed below.
The Manufacturer shall design, supply and assemble the flange adapter,
the flexible joint between motor and gear.
With the Offer the Supplier of the Gears must supply the complete
technical description of the gear boxes with the details of the coupling and
flange for the motor, at present estimated to be the 160 L Size of the
European Standard.
1.2 Motors
The 8 motors (plus one spare) will be:
- squirrel cage motors, continuous duty
- totally enclosed
- class F insulation
- 460 VAC, 60 Hz, 3-phase Delta
- 20 HP (15 kW)
- 1800 rpm nominal speed
- flanged in vertical position
- brake
- integral mount to motor
- disc type
- 24 VDC fail safe operation (brake engaged with power off)
- capacity 81 Nm (60 Ft-lb)
- external cooling blower
- single phase, 60 Hz
- controlled by brake control output
- thermal protection by temperature sensors against overheating
The verification of the motor size and the cooling blower size has to
be done by the Manufacturer taking into account of the environmental
conditions where the enclosure shall be installed, as listed below.
With the Offer the Supplier of the Motors must supply the complete
technical description of the Motor complete with the DC disc brake.
1.3 Inverters
Each of the 8 motors shall be powered by a variable frequency drive (VFD)
for controlling the motors from 1,2 up to 60 Hz at constant torque.
Alternately, pairs of motors on the same bogie could be controlled by
a single inverter.
The Supplier shall verify the necessary nominal rated power of the
group and the eventual necessity of controlling it in temperature for
the operating conditions listed below. The system can be asked to
perform the equivalent of a continuous duty cycle at the nominal
torque and at the minimum speed corresponding to 1/50 of the nominal
one. The characteristics of the inverters should be:
- 460 VAC, 60 Hz, 3-phase Delta
- 1,2 - 60 Hz frequency range (with programmable maximum frequency)
- constant torque output
- 20 HP output capability per inverter using 8 inverters
(or 40 HP per inverter if only 4 inverters used)
- programmable acceleration/deceleration rates
- brake control output
- Site Elevation over the sea level: +3200 m (10500 feet)
- Storage temperature: from -30 up to +50 C
- Operating temperature: from -15 up to +25 C
- Storage pressure: from 500 up to 760 Torr
- Operating pressure: from 500 up to 600 Torr
- Storage humidity: from 5% up to 80%
- Operating humidity: from 5% up to 95%
3.1 Delivery Time
If the motors and inverters are to be supplied by an independent manufacturer,
they should be delivered to the Supplier of the Gear Reduction Units by 10
January 1998.
Each Gear Reduction Unit shall be supplied completely assembled (and
tested) with the relevant motor to the Bogie Manufacturer's
(Costamasnaga) workshop within the 31 January 1998. Shipping costs are
to be included in the Supply.
3.2 Delivery Location
The driving units, completely assembled and tested must be delivered to the "LBT Corporation, c/o Osservatorio Astrofisico di Arcetri" at the following address :
COSTAMASNAGA S.P.A.
Via IV Novembre n. 2
Costa Masnaga, Lecco
ITALY
telephone:39-31-858111
telefax: 39-31-879332
After assembly with the Bogies, these units will be exported to Mt. Graham
in Arizona to be installed on the enclosure of the Large Binocular Telescope.
Doc_info_start
Title:Technical Specification for Rotating Enclosure Motors and Gears
Document Type:Technical Specification
Source:ADS Italia Srl
Issued by:W. Gallieni & S. DeRigne
Date_of_Issue:11-05-97
Revised by:J. M. Hill
Date_of_Revision:11-05-97
Checked by:W. Gallieni
Date_of_Check:09-22-97
Accepted by:
Date_of_Acceptance:
Released by:
Date_of_Release:
File Type:HTML
Local Name:
Category:Rotating Enclosure
Sub-Category:General Rotating Enclosure
Assembly:Rotating Documents
Sub-Assembly: Gears and Motors Technical Specification
Part Name:
CAN designation:301s001
Revision:A
Doc_info_end
Last modified: Wed Nov 5 16:11:10 1997